How Robots Can Be Used to Improve Workplace Safety and Productivity
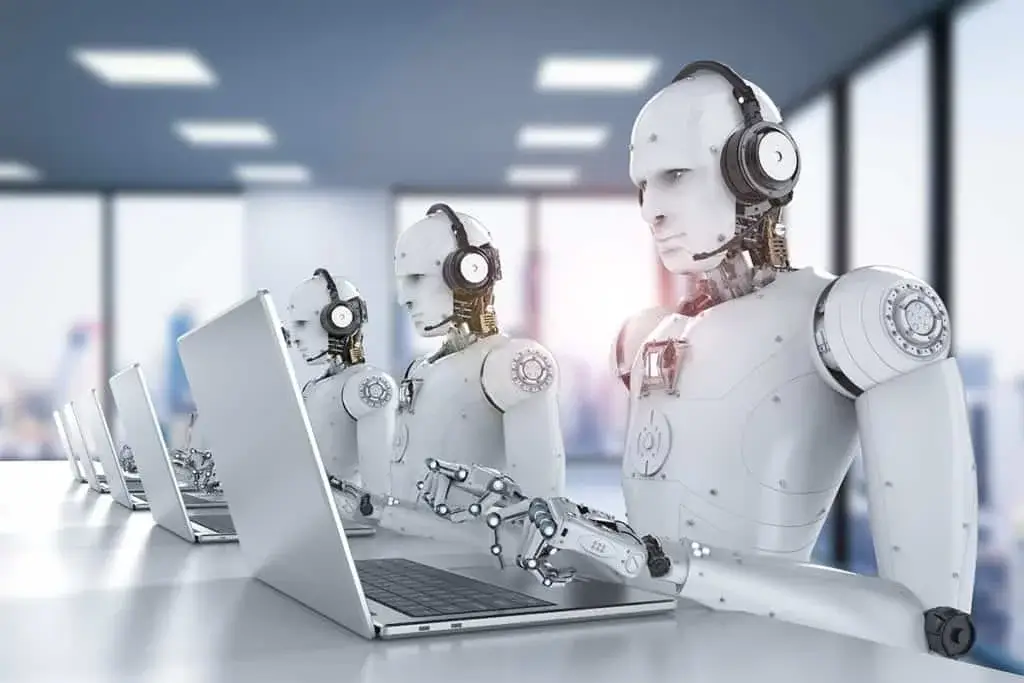
For workers in highly dynamic environments, robots are an excellent way to reduce fatigue and distraction. These robots can be either hand-guided or computer-controlled and can be used to complete tasks under the direct control of a worker. Robots can also handle hazardous materials or machines. Manufacturing jobs are notorious for involving significant safety risks, which increase the risk of injury and complacency. In addition to these concerns, robots can also help to prevent long-term health complications.
Cobots reduce fatigue related errors
In the workplace, cobots can improve productivity and increase efficiency. These machines are designed to help human employees perform repetitive and mundane tasks. These machines are capable of performing tasks with minimal human input, such as cleaning, filing, and assembling products. In addition, they do not have the potential for motion injuries and are not susceptible to fatigue. When cobots are used to complete mundane, backbreaking tasks, humans can focus on other more complex tasks.
Human workers have to exert a lot of force when they do their finishing tasks. This can be dangerous and cumbersome. Cobots can provide the required force without the risk of injury and can handle the finishing tasks with precision and accuracy. In addition, cobots are programmable to perform tasks based on the dimensions of each part. This feature is invaluable for reducing fatigue related errors in the workplace.
When working with soft-stemmed plants, cobots can assist in the handling of plants. The compact structure of these machines doesn’t require a large space for installation. A cobot arm grabs a pipe from a loading mechanism, moves it to the casing, and then unloads it. All this happens in ten seconds. As a result, the cobot’s installation doesn’t require a redeployment of production lines, and cobots are flexible and universal. Their costs have been recouped in ten months.
Single-task robots reduce distractions
One of the many benefits of single-task robots is their reduced workload. These robots can do boring, repetitive motion jobs and will not cause stress to workers. Furthermore, these robots can be used in areas where employees may find themselves distracted, such as the workplace. Aside from reducing employee distractions, single-task robots can also increase the company’s productivity. One example of this is when robots help in warehouse operations. They can move hundreds of cases per hour.
To test this, researchers have found that a robotic assistant can increase workers’ cognitive performance by displaying non-verbal cues, such as facial expressions or body language. The study has also found that when people interact with a robot, they are more likely to follow its suggestion. The study also found that a robot with a complementary personality can be more appealing to workers than an extroverted one.
When a worker performs a familiar task, he may become distracted by a variety of factors. Performing too many tasks at once can lead to errors. In addition, under time pressure, workers may make mistakes that result in violations. With robots, there are fewer mistakes because the robot will be doing a repetitive motion and not a random act. With this kind of flexibility, single-task robots can help workplace safety in many ways.
Cobots improve worker safety in highly dynamic environments
The use of cobots in manufacturing environments has several benefits for workers and employers alike. These automated machines do not require a skilled workforce or specific training, and they are capable of shoulder-to-shoulder deployment next to humans during busy seasons or temporary tasks. They can perform complex tasks with minimal downtime, including assembly, packaging, and palletizing. And they can fit into confined spaces, too. Workers are freed from repetitive motion and heavy lifting, which can lead to repetitive stress injuries.
Although some workers were hesitant to accept cobots at first, today employees can’t imagine life without them. Staff members have affectionately nicknamed their robots Thelma and Louise. The UR10 robotic arms are so low-cost, staff is constantly searching for ways to improve processes and efficiencies. They’re also looking for new ways to use cobots in their workplaces.
As a human-like machine, cobots operate more like humans. They work at a slower pace and lift payloads similar to human workers. But because traditional industrial robots move faster and have more power, they can be a serious threat to unprotected workers. That’s why they often need additional safety measures such as fencing and other barriers to prevent accidents. So how can cobots help your company?
MiR AMRs reduce fatigue related errors
The company behind MiR AMRs believes that its innovative technology can improve worker safety and productivity. MiR AMRs are highly flexible and integrate seamlessly with human workers, which reduces risks of human error. The company also emphasizes the importance of cloud connectivity, which is essential to AMRs’ ability to navigate complex environments. In this article, we’ll look at how MiR AMRs can help businesses improve worker safety and productivity.
AMRs are able to perform a variety of tasks, which can be non-ergonomic and lead to musculoskeletal problems. Even 10 pound parts can become heavy after several hours, resulting in injuries, lower product quality, and human error in operating machines. Because of these benefits, AMRs are also valuable in packaging operations. They can be programmed to perform multiple tasks in the same facility, resulting in a higher degree of accuracy.
Exercise has a variety of effects on circulating miRNAs. They may serve as biomarkers of PEM and may be useful therapeutic targets. For example, hsa-miR-181b-5p is thought to play several roles in adapting to physical efforts. In one study, Shah et al. found that acute exercise increased hsa-miR-181b-5p levels in plasma and skeletal muscle tissue.
Human-machine interfaces
In addition to being a useful tool to increase safety and productivity in the workplace, HMIs also have several other advantages. They can reduce the total cost of hardware by replacing dozens or even hundreds of separate indicator lights. This means less space is needed for unnecessary hardware. Another benefit of HMIs is that they improve usability by reducing the learning curve. However, a successful HMI must be designed with the end user in mind.
A well-designed human-machine interface can compensate for changes in physical performance and sensory impairment. Supplementary lighting can provide greater brightness to older users, and high contrast on displays can help the visually impaired. It can also be used to adjust acoustic signals from machine functions to ensure equal hearing by young and old users. These factors help make a well-designed human-machine interface more effective in reducing health complaints and ensuring that machines are as safe as humans.
Human-machine interfaces are becoming increasingly common in the workplace. Improper human-machine interfaces can lead to serious accidents and diseases. Therefore, proper design of workplaces and equipment must address the needs of human users and workers. This report will examine how human-machine interfaces influence occupational risks. And in the meantime, it will help employers design safer workplaces for their employees.
Safety requirements for robots
One of the primary requirements for a safety program for a robot is the ability to recognize malfunctions and implement corrective measures. This includes educating employees on proper robot operation and recognizing the hazard associated with a malfunction. In addition, the operating program should account for the cumulative mechanical failure that may occur over time. When a robot malfunctions, it should be possible to immediately cut off power to prevent the arm from flinging a work piece.
OSHA guidelines for robotics in the workplace require that facilities implement lockout/tagout (LOTO) systems to ensure that the robots are not switched on when not in use. In one recent case, a Nissan plant was fined $12,675 for inadequate training of its workers in the proper use of LOTO. Additionally, robotics manufacturers must adhere to existing OSHA standards for programming. Robots should only be programmed to perform pre-programmed tasks and not stray off the job site.
In addition to the installation of physical barriers, safety systems for robotic workstations should also include guarding systems. These can include gate guarding systems that stop robotic operations if a human enters the fenced area. Another important feature of a safe robotic workstation is the installation of presence-sensing devices such as light curtain installations, pressure floor mats, and ultrasonic sensors on the robot’s arm. It is ideal to install multiple presence-sensing devices within the workstation. Lastly, the robotic controls should be in a separate location from the robot’s work area. This way, employees will never accidentally operate the controls.